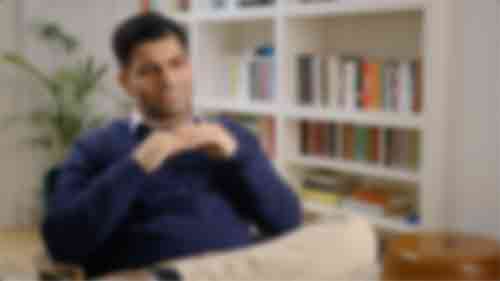
Sorting & Picking
Former VP, Amazon Logistics Europe
inpractise.com/articles/amzn-sorting-picking
Why is this interview interesting?
- How Amazon organize warehouses and sorting and picking processes inside the warehouse
Philippe Hemard
Former VP, Amazon Logistics Europe
Interview Transcript
Inside the warehouse and picking and sorting, can you just outline the principles that Amazon use, to organize inventory, inside a fulfilment center?
Amazon has different types of buildings, which are mostly linked to the type of product or, at least, the size of the product. Amazon has a big split between what they call sortable and non-sortable. Roughly, the sortable is 30cm by 30cm by 40cm. It’s a large box, just below a microwave oven box. This is sortable, because it was meant to go on a conveyor, whereas the others were too large for that. It’s a purely arbitrary choice, which was made, very early, by Amazon, based on the sub-optimization that they had. Therefore, in the Amazon network, you have sortable buildings and non-sortable buildings. In non-sortable building, most likely, there are racks and they can manage large sized boxes, which can sometimes be heavy.
There is a third category that they call the heavy-bulky, which are most likely to be washing machines and fridges and stuff like that. It is definitely two-man handling and sometimes, even needs to be handled by equipment. Those are the three main categories.
Amazon has also segregated the last one, which is shoes and apparel. There is a very specific fulfilment or storage method. That’s upstream. Each of the buildings, after that, they are pretty much the same, for each type of the product. The biggest part is still the sortable. More than 85% to 90% of what is sold by Amazon is sortable, so you will find a huge number of sortable sites. Those are still the typical products for Amazon, because they started with books. They have shelves, mostly, multi-story shelves, where the people walk into, to pick up the products. The shelves could be different sizes – there is a small shelf and a large shelf. They have a few pallets, as well and they also have some pallet racks, for replenishment, for the high-rotation ones. That is the structure for sortable.
For non-sortable, there are a lot fewer shelves. There are some shelves, because some large products can still go on shelves, but mostly, it will be pallet racks or pallets on the floor. More traditional picking like you could find in any traditional warehouse. The heavy-bulky will sometimes be with mass pallets and no racks, for the very large items. Of course, when you understand that volume, as I say, 85% to 90% being sortable, the non-sortable are larger, because of the huge volume. In terms of space, it might be today, in Amazon that 50% of the sites are sortable and 50% are non-sortable, because of the space taken up by the products, in each category.
That is how it is organized. Inside, you have a receive area, which is pretty common again, adapted to the products. For the sortable, you have conveyors and people are putting the products on a conveyor, which go in this big tower. In non-sortable, it’s done more by forklift. That’s the major difference.
The ultimate change, which came later, was the automated side and the less automated side. There are a few historical manual sites, where people go around, even with carts. There are still some of them and they are more than 10 or 15-year-old. The new ones are the Kiva enabled sites, where nobody really goes in the big tower. The robots go to the shelves, to pick up the product and bring to the people.
Copyright Notice
This document may not be reproduced, distributed, or transmitted in any form or by any means including resale of any part, unauthorised distribution to a third party or other electronic methods, without the prior written permission of IP 1 Ltd.
IP 1 Ltd, trading as In Practise (herein referred to as "IP") is a company registered in England and Wales and is not a registered investment advisor or broker-dealer, and is not licensed nor qualified to provide investment advice.
In Practise reserves all copyright, intellectual and other property rights in the Content. The information published in this transcript (“Content”) is for information purposes only and should not be used as the sole basis for making any investment decision. Information provided by IP is to be used as an educational tool and nothing in this Content shall be construed as an offer, recommendation or solicitation regarding any financial product, service or management of investments or securities.
© 2025 IP 1 Ltd. All rights reserved.