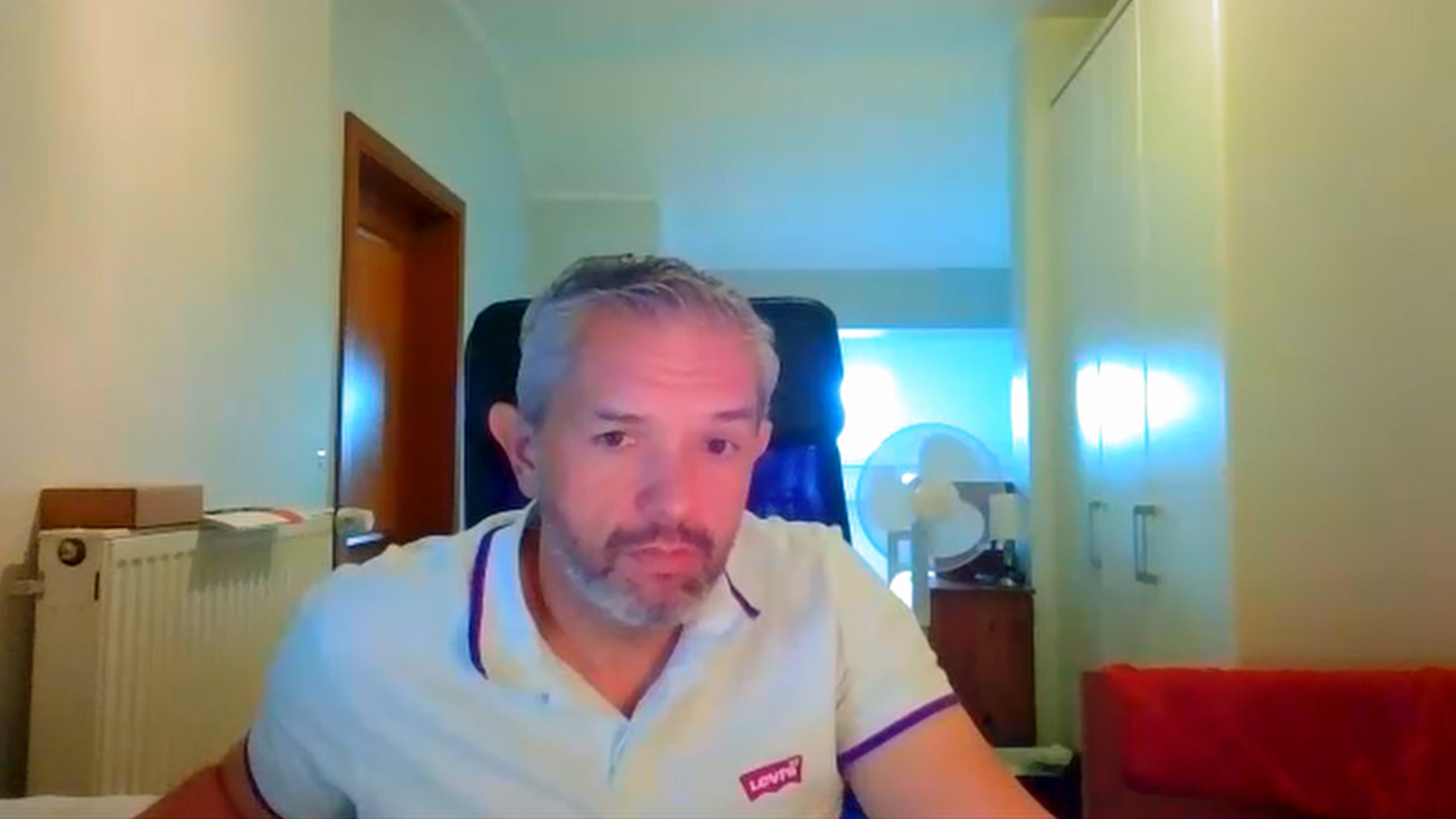
Inbound & Outbound Unit Costs
Former VP, Amazon Logistics Europe
inpractise.com/articles/amzn-cost-structure
Why is this interview interesting?
- Breakdown of Amazon’s inbound and outbound costs
Philippe Hemard
Former VP, Amazon Logistics Europe
Interview Transcript
Before we move onto the last mile, when you look at the whole process, from order to shipping and delivery, what is the split in the total cost of the package and delivery? Is it 10% on inbound, 20% on picking and 70% on outbound? How do you look at where the cost and real challenge actually lies, in that process?
Firstly, it depends if you talking about fulfilment cost or the total cost, including picking up at the vendor and delivering to the customer. The in-the-box cost, from the door of the fulfilment to the outbound door of fulfilment, roughly 30% is spent in inbound and 70% in the outbound, of the total cost of process. It depends; it could be 25%:75%. Two thirds of the outbound is going to be the packing and shipping activity and one third is going to be the picking, roughly.
Again, that really depends on which type of building. It will vary a lot, depending on if there is a Kiva system, where there is a little bit less time spent in picking. There is a merge between picking and storing, because the same people are doing both, so that’s blurred a little bit. But roughly, I think, it would be that split, so 50% is in the packing and shipping.
Which is where scale matters?
I don’t know. The picking is where scale matters the most, or the density. We mentioned the density in delivery and the density in picking is one of the keys. Whether you are in automated or not, it’s still an optimization, because if you are in manual, that matters a lot, because that is the time that the picker has got to spend in walking, from location to location. But even when you are automated, it matters. The less movement that the robots are doing, the more movement they can do and the less distance they cover, the more available they are for the next pick. Therefore, if you can bring your shelf to a picker and have 15 items to pick at the same time, on the shelf, it’s better than having a shelf and pick one and having to then bring another one. The productivity will be better. Picking is maybe where the density matters most. Not the size because, of course, the bigger you are, the more challenging are your pick paths. But if you have a lot of volume, that’s where it matters.
For the rest, a little bit less, because the storing is random and so people are storing in the same area. When they go, they store and, as they don’t have any rules, they just store in the same area and they don’t move much. For the packing, in that case, no. It is not the case that if you have 10 packing tables it will go faster than one packing table on its own. For the whole organization, yes. With the conveyor, automatically loading trucks, those kind investments which could ultimately help in lowering your costs.
Copyright Notice
This document may not be reproduced, distributed, or transmitted in any form or by any means including resale of any part, unauthorised distribution to a third party or other electronic methods, without the prior written permission of IP 1 Ltd.
IP 1 Ltd, trading as In Practise (herein referred to as "IP") is a company registered in England and Wales and is not a registered investment advisor or broker-dealer, and is not licensed nor qualified to provide investment advice.
In Practise reserves all copyright, intellectual and other property rights in the Content. The information published in this transcript (“Content”) is for information purposes only and should not be used as the sole basis for making any investment decision. Information provided by IP is to be used as an educational tool and nothing in this Content shall be construed as an offer, recommendation or solicitation regarding any financial product, service or management of investments or securities.
© 2025 IP 1 Ltd. All rights reserved.